DMAIC
DMAIC is a structured approach to improving processes and solving problems. It stands for Define, Measure, Analyze, Improve, and Control, and is used by businesses to improve efficiency and reduce defects. This method is used to improve processes by identifying and removing defects and reducing process variation.
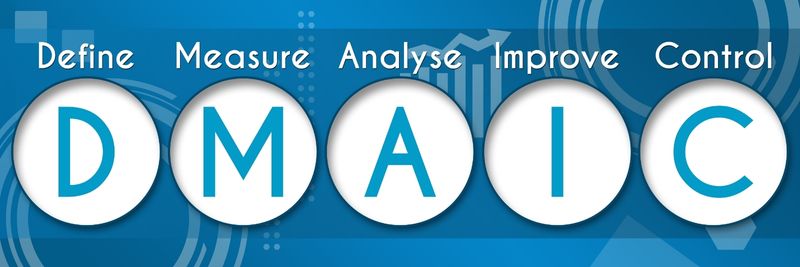
In the Define step, you identify the specific issue to address and the goals and objectives of the improvement project. Clearly defining the problem keeps the project on track and helps achieve its desired outcomes.
The Measure step involves collecting and analyzing data to understand the problem and its impact on the business. You identify the key performance indicators (KPIs) to measure the project’s success and determine the baseline performance of the process.
During the Analyze step, you use the data from the Measure phase to identify the root causes of the problem. You use tools like cause and effect diagrams and statistical analysis to identify the underlying factors contributing to the issue.
The Improve step focuses on implementing solutions to address the root causes identified in the Analyze step. You develop and test potential solutions, select the best ones, and implement them in the process.
In the Control step, you monitor and maintain the implemented solutions to ensure they continue to produce the desired results. You establish control mechanisms, such as ongoing monitoring and data analysis, to ensure the process remains stable and continues to improve.
DMAIC is a powerful tool for improving business processes and improving quality. By following the methodology, organizations can systematically identify and address defects in their processes, leading to increased efficiency, reduced costs, and improved customer satisfaction.